Top Strategies for Optimizing Steel Fabrication Processes for Maximum Efficiency
From thorough design planning to accepting advanced modern technologies, the mission for optimal effectiveness in steel fabrication includes a multifaceted technique. Let's check out just how these methods can revolutionize steel construction procedures, paving the means for unprecedented effectiveness and competitiveness in the market.
Reliable Design Preparation
In the realm of steel construction procedures, strategic and effective design preparation plays a critical duty in streamlining production operations and optimizing operational productivity. The design of a steel manufacture facility directly affects the performance of procedures, material flow, and worker performance. By meticulously developing the plan of equipment, workstations, storage space locations, and product handling equipment, business can substantially lower unneeded movement, minimize material managing times, and enhance the total manufacturing procedure.
An efficient layout plan considers elements such as process series, distance of workstations, product handling routes, and security laws. It aims to develop a streamlined and rational flow of activities from basic material intake to the end product send off. Via reliable layout planning, business can eliminate bottlenecks, reduce manufacturing downtime, and boost the total functional effectiveness of the steel construction process.
Additionally, a well-thought-out layout plan makes it possible for much better use of offered area, improved interaction in between workers, and enhanced safety techniques within the center. In general, investing time and sources in creating an effective layout strategy can produce considerable advantages in regards to enhanced productivity and price savings for steel fabrication organizations.
Advanced Reducing Technologies
Using cutting-edge modern technologies in steel construction processes boosts precision, performance, and general production high quality. Advanced cutting modern technologies play a critical function in streamlining procedures and optimizing the manufacture process. Among the most famous developments in this area is the implementation of laser reducing systems. Laser cutting deals unrivaled accuracy, enabling complicated forms and elaborate layouts to be cut with very little product wastage. Furthermore, plasma reducing technology has actually additionally transformed steel manufacture by enabling swift and accurate puncturing electrically conductive products. This approach is specifically effective for cutting thick steel plates with rate and precision. Water jet cutting is another ingenious modern technology that uses a high-pressure stream of water to cut via numerous sorts of materials, consisting of steel, with extraordinary accuracy. By including these advanced cutting innovations right into steel manufacture processes, producers can substantially raise efficiency, reduce production times, and eventually improve the high quality of their items.
Automated Welding Systems
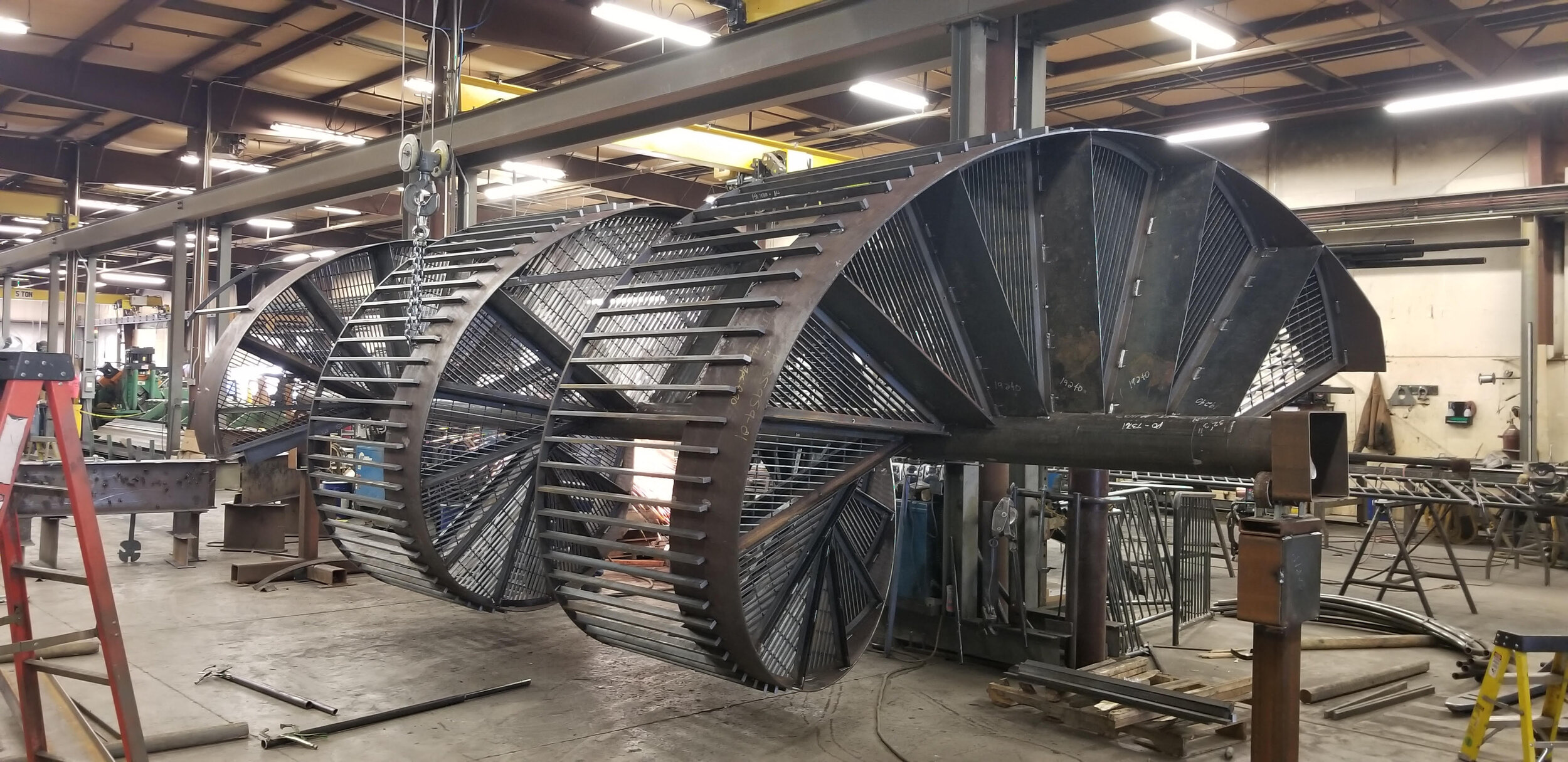
Among the key benefits of automated welding systems is their ability to preserve a high level of accuracy throughout the welding procedure. The precision supplied by these systems guarantees that welds are consistent and meet the called for specifications, causing stronger and a lot more reliable steel frameworks. Furthermore, automated welding systems minimize the risk of human mistake, causing fewer issues and rework.
Moreover, these systems can handle complicated welding jobs with ease, including welding in limited rooms or on curved surfaces. This convenience makes automated welding systems suitable for a large range view website of steel fabrication applications, from massive commercial tasks to intricate customized styles. On the whole, the implementation of automated welding systems in steel construction procedures dramatically improves efficiency, quality, and general job end results.

Supply Monitoring Solutions
Enhancing operational performance and simplifying procedures, reliable supply monitoring remedies play a crucial duty in maximizing steel manufacture procedures. By applying durable stock administration systems, steel construction companies can guarantee that the right products are readily available when required, lessening interruptions and delays in production timetables. Making use of sophisticated software application services enables real-time monitoring of supply levels, enabling exact projecting of material requirements and protecting against stockouts or overstock scenarios.
Additionally, inventory monitoring options assist in reducing lugging expenses related to excess supply and enhance capital by lining up inventory degrees with actual need. By categorizing products based on use frequency and criticality, producers can prioritize purchase and storage space appropriation, additionally enhancing functional efficiency. In addition, executing barcode or RFID technology assists in accurate stock tracking and simplifies the surveillance of material activities within the find facility.
Continual Process Enhancement
To construct upon the gains made with reliable inventory administration solutions, the focus now changes in the direction of driving continuous process enhancement within steel fabrication procedures. Continuous procedure improvement is a systematic approach targeted at improving performance, reducing waste, and boosting total quality throughout the construction procedure. By implementing a culture of continual improvement, steel fabrication business can recognize traffic jams, streamline process, and enhance sources to make the most of efficiency.
One trick aspect of continuous process enhancement in steel construction is the normal testimonial and analysis of manufacturing procedures. This involves gathering feedback from employees, keeping an eye on vital efficiency indications, and recognizing locations for improvement. By leveraging data-driven understandings, firms can make informed choices to drive meaningful changes that positively impact operations.
Moreover, adopting lean production concepts can dramatically add to refine renovation in steel manufacture. try this web-site Alpha reo. Techniques such as worth stream mapping, five company, and Kaizen events can help eliminate non-value-added tasks, systematize procedures, and promote a culture of development and continuous learning within the company
Verdict
Finally, enhancing steel manufacture processes for optimal performance requires cautious preparation, making use of advanced cutting modern technologies, implementing automated welding systems, handling stock properly, and continuously improving processes. By including these approaches, manufacturers can enhance efficiency, lower prices, and enhance overall performance in the steel construction market.
With reliable format preparation, firms can eliminate bottlenecks, reduce production downtime, and enhance the general operational effectiveness of the steel construction procedure. steel fabrication melbourne.
Utilizing cutting-edge innovations in steel manufacture procedures enhances precision, effectiveness, and overall production top quality. By integrating these advanced cutting innovations into steel fabrication processes, suppliers can significantly boost performance, reduce manufacturing times, and eventually boost the quality of their products.
Generally, the implementation of automated welding systems in steel construction processes significantly boosts effectiveness, top quality, and total job results.
One key aspect of continual process improvement in steel manufacture is the normal evaluation and analysis of manufacturing processes. (steel fabrication melbourne)